H2Use Successfully Demonstrates First-Ever Biconvex Hydrogen Airship
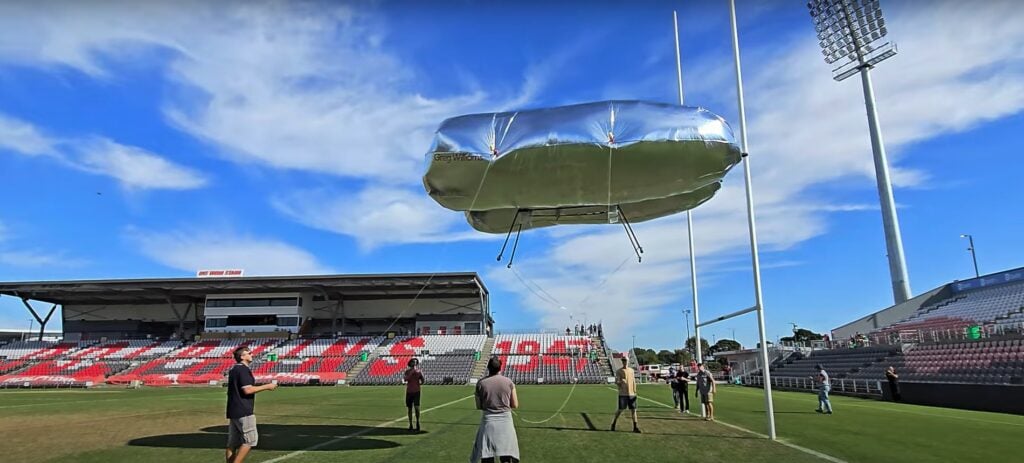
Redcliffe, Queensland — May 25, 2025
In a landmark moment for the future of sustainable aviation, the H2Use team launched and flew the world’s first biconvex hydrogen-powered airship at the Dolphins NRL Kayo Stadium in Redcliffe, Australia. The event, marking the culmination of over four years of grassroots innovation, captured both the imagination and admiration of a growing community invested in the revival of lighter-than-air flight.
A New Shape for a New Era
The H2Use prototype broke with more than a century of airship tradition by using a dual-hull, biconvex envelope design. This distinct departure from the classic cigar-shaped body wasn’t simply aesthetic—it was a strategic engineering choice. The dual hull concept is intended to maximize internal volume while offering superior aerodynamic stability and compactness, dramatically reducing the “wobble” often associated with traditional blimps.
Most importantly, the biconvex profile allows the airship to fit within the A380 “box” size, opening the possibility of servicing at any facility designed for Airbus A380 aircraft—an unprecedented advantage in airship logistics.
Powered by Hydrogen, Guided by Precision
The H2Use airship draws its lift and propulsion power entirely from compressed hydrogen. A hydrogen fuel cell converts the gas into electricity, which then powers an array of electric ducted fans (EDFs) mounted within a central carbon-fiber duct. These EDFs are mounted on gimbals, allowing vectored thrust in multiple directions—eliminating the need for traditional control surfaces like rudders and elevators.
Complementing this advanced propulsion system is a water ballast control system, operated via solenoid valves for real-time balance adjustments. The airship’s structure, made with carbon fiber, additive manufacturing techniques, and mylar-based envelopes, embodies a fully modular, lightweight philosophy.
The Flight: Triumph, Turbulence, and Learning
The demo flight, attended by engineers, safety officers, media, airship veterans, and local supporters, was a spectacle of both technological promise and real-world lessons. Lifting off cleanly and hovering stably at ~5 meters, the airship demonstrated effective maneuverability using its vectored EDFs. However, a slow hydrogen leak in the port-side envelope introduced an imbalance mid-flight, prompting a cautious return.
While preparing for a secondary sortie, structural stress during refueling caused the gondola to separate from the main envelope—a critical mechanical failure. Not to be deterred, the team opted for a symbolic “field promenade” of the now uncrewed envelope. But fate had other plans: the envelope caught a gust of wind and lifted off unexpectedly, drifting 21.4 km eastward over Moreton Bay before being recovered by a ferry crew hours later.
More Than a Prototype: A Platform for the Future
Despite the dramatic conclusion, the flight succeeded in its primary mission: validating the feasibility of a biconvex, hydrogen-powered airship. All key systems—including hydrogen fuel cells, electric thrust, ballast management, and vectored control—performed to spec.
The H2Use initiative is more than a single aircraft—it’s a modular platform, akin to LEGO in spirit. With a gantry-operated, swappable gondola, the airship can be rapidly adapted for multiple use cases: scientific research, surveillance, humanitarian aid, or light cargo. The team envisions third parties customizing payloads while they provide the flight-ready platform.
What’s Next: Phase II and the “Zippy” Prototype
Building on the lessons of the first flight, the team is now deep into Phase II, developing a more durable prototype named Zippy. Designed with real-world missions in mind, Zippy will boast:
- Envelope Volume: 2,500 m³
- Dimensions: 15m x 8m x 5m
- Flight Time: Up to 7 days
- Range: 2,000 km (round trip)
- Payload: 500 kg
- Cruising Speed: 70 km/h
The Zippy prototype will incorporate polyurethane-based materials, improving structural reliability. Other enhancements include solar-assisted hydrogen recovery and improved tracking systems.
Join the Journey
Currently composed of a ten-member interdisciplinary team—including experts in aerospace engineering, materials science, hydrogen systems, additive manufacturing, software, and flight operations—H2Use is actively seeking engineers, students, and volunteers to contribute to Phase II. Those interested are encouraged to connect via the project’s website.
Open Innovation and Transparency
H2Use also intends to open-source portions of their work, including 3D models, control systems, and hydrogen management schematics. This move is designed to foster innovation, community feedback, and potentially accelerate the development of airship technology worldwide.
The skies may have claimed the first prototype, but H2Use has proven something far more enduring: the dream of sustainable, hydrogen-powered airship flight is no longer fantasy—it’s airborne.
To learn more or to get involved, visit: https://h2use.com/2025/05/26/h2use-airship-phase-i-the-big-story/
Responses